Defense and Military Aerospace Manufacturing
PAR Systems develops custom advanced manufacturing equipment that supports a wide array of defense applications. Many of our systems apply OUSD Critical Technologies and provide efficiency, adaptability, and exceptional performance to even the most demanding applications.
Supporting Our Customers with OUSD Critical Technologies
Our innovative technologies and developmental approach make us highly effective partners in these areas of Office of the Under Secretary of Defense for Research and Engineering [OUSD(R&E)] critical technologies areas:
- Advanced Materials—We design and develop custom and novel manufacturing techniques to dramatically improve strength, weight, efficiency, and performance across extreme temperatures. Our patented Friction Stir Welding systems can efficiently weld high-strength alloys required for challenging environments.
- Trusted AI and Autonomy—Our solutions utilize the latest AI technologies to improve anomaly detection, part identification, and overall system efficiency. In addition, PAR implements robust monitoring to enable real-time quality inspection and reduce or eliminate post process requirements.
- Space Technology—As a leader in space manufacturing, we provide friction stir welding solutions used in the manufacturing of high-performing cryogenic fuel tanks; we automate application of foam insulation, increasing throughput and reducing waste; and our specialty crane systems are designed for critical, extremely high capacity hoisting applications.
- Renewable Energy Generation and Storage—We are a leading technology provider for the production of cryogenic tanks utilized in the storage and transportation of hydrogen. Our high-precision, high-capacity crane systems with nuclear-rated safety facilitate unique material handling requirements associated with renewable energy applications.
Experts in Advanced Manufacturing Equipment for Defense Applications
Fastening
PAR integrates proven tools into automated end effectors along with appropriate sensors and intelligence to perform fully automated fastening operations. Automated fastening systems provide a number of benefits, including:
- Reduction of man-hours and costs while improving productivity
- Solving the many challenges created by variabilities that occur with incoming materials
- Combining processes in a single work cell to include scanning, prepping, and painting to reduce manual operations and maximize real estate on the manufacturing floor
- Optimizing accessibility in confined spaces normally associated with specialized military aircraft
Configurable, Robotic Fixtures
Configurable, robotic fixtures from PAR provide easy accommodation of design changes and the addition of new parts while maintaining quality using adaptive manufacturing techniques. This eliminates costs and time of management, handling, storage, and introduction and removal of dedicated tools in your application. We apply this technology to missile assembly, where high adaptability in the production line is needed as new revisions are made, and by repurposing existing capital equipment, time from design to to initial operating capability (IOC) is reduced.
Waterjet Cutting
Waterjet cutting systems provide highly controlled, precise cutting of parts. This process eliminates the potential for material distortion from heat. Our waterjet cutting systems can also operate in up to 5 axes of motion and can be customized to suit any application, making it well suited for cutting carbon fiber materials, such as aircraft stringers and space launch fairings. We also provide fully integrated systems that include part geometry verification and automated part and tool loading. PAR’s ability to build highly-customized, large, and highly precise waterjet cutting solutions provides unique value to Aerospace and Defense manufacturing solutions.
Friction Stir Welding
Friction stir welding is a solid-state joining process for high-strength alloys (such as aluminum, titanium, and steel). Friction stir welds are high quality, lighter weight with fewer defects and voids, no foreign object debris, and conducive to an automated process, meaning it is not as reliant on an operator to perform a quality weld. This makes FSW the ideal choice for welding components of ground defense vehicles and other vehicles or structures where quality is paramount. PAR’s precise, data-driven I-STIR™ FSW System efficiently produces highly durable welds that perform exceptionally under testing, and our advanced controls enable the adoption of Machine Learning to further improve weld quality and manufacturing throughput for complex defense vehicles.
Automated Assembly
Using the latest technology in vision, motion control, and component handling, PAR has automated processes from sorting and feeding to assembly and part inspection. Significant improvement in cycle time, reduced labor costs and improved productivity are just the beginning. Leveraging decades of experience assembling medical devices, PAR is adopting this technology to the manufacturing of small aerospace components, such as missiles and armament, where precision and finesse are essential. PAR’s automated assembly technologies offer many additional benefits including:
- Consistent quality of finished goods and accurate assembly
- Rapid integration using our standard software for many common functions
- Automated logging with 21 CFR part 11 compliance
- ISO 9001 and 13485 certified project management and documentation approach
Other Advanced Solutions for Defense Applications:
Specialty Applications in Defense Manufacturing
The PAR Advantage.
At PAR Systems, expertise, experience, technology, and a custom approach combine to create innovative, effective solutions for defense manufacturing.
Through our worldwide service organization, we also offer dedicated support from a team of local field service engineers, and our global consulting team can resolve the most complex engineering challenges.
For more information, read about our ongoing partnership with NASA, or speak with one of our experts about your defense manufacturing project.
Our expertise shows in each element we craft.
Certified in all the right places.
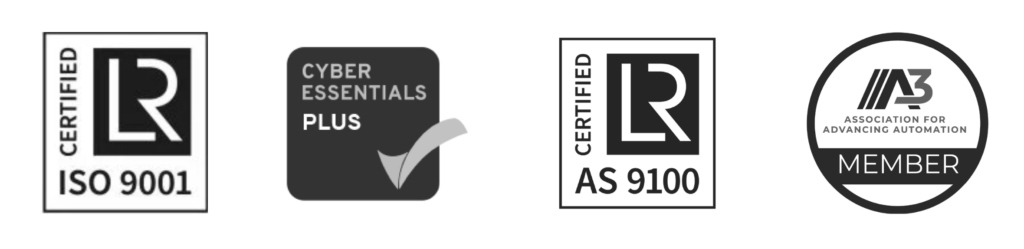